A while ago I was approached by Overhanglab.com (QTS) about whether I would be interested in trying out their resins. I usually resist testing resins since, in my experience, most of the smaller companies just blindly copy the original resin formula by Autodesk and they are the same rubbish as Elegoo and Anycubic Standard resins: not particularly strong and very brittle. However, QTS gives some really strong claims about their resins, so I thought – let’s see if they are true or just a marketing talk.
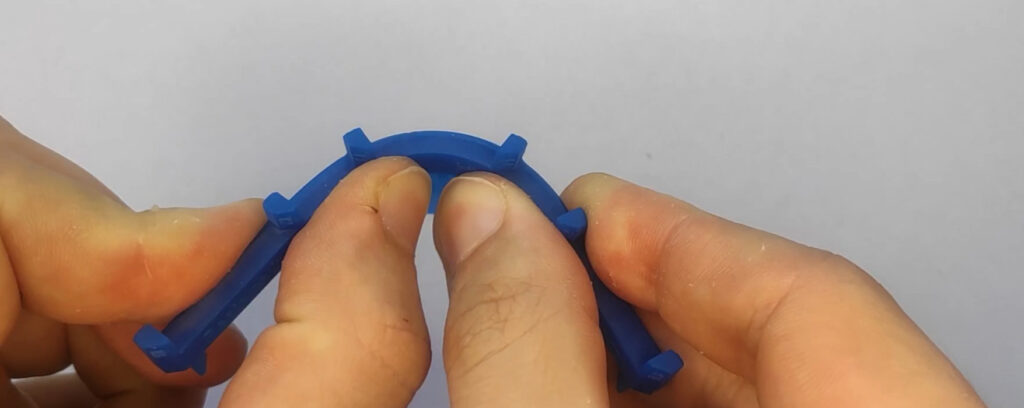
I had the opportunity to test their Model resin, Flex resin, Engineering Strong resin, and Engineering High Temperature. In this post, I will share my experience with all of them except for the high-temperature one. The high-temperature one needs further testing and I have an exciting project with it on my mind which deserves a blog post on its own. Let’s dive in.
To be clear; I received a sample of their resin for free. But I wasn’t paid for the review and all opinions presented in this post are mine.
Flex resin
The first resin we will look at is their Flex resin. It claims to have a hardness of Shore A 57– that’s pretty soft. It is a translucent liquid with the consistency of maple syrup. It has no particular smell. Printing the resin is easy compared to other flexible resins I have tried (especially due to its low viscosity). During my experiments, I have, however, come to several guidelines that help you get a successful print:
- If you can, print flat on your build plate as the resin’s flexibility doesn’t play nice with supports.
- When you need to use supports, I had to use relatively thick supports (I used 2.5mm diameter and 1.3mm tip)
- If you can, use PFA instead of FEP. This resin sticks much less to PFA and thus the model doesn’t bend as much during printing.
The printed models get a slight yellow tint, but even after curing, they stay nice and flexible. The flexibility is not given by the models being thin. Even a thick tire model (which is not hollowed) is flexible. See the videos below.
The resin isn’t super strong. Don’t get me wrong – it isn’t fragile and it doesn’t break easily. You just can’t expect the same strongness as, e.g., silicones. I also don’t think it is a suitable resin as an additive to other resins in order to increase toughness. There are better resins for that – e.g., the Model resin which I will introduce later.
Nevertheless, I am pleasantly surprised by this resin. It is the most flexible resin I have worked with and unlike the other ones, it is actually relatively painless to print.
Engineering strong
I am always looking for strong and durable resins that I could use to prototype functional parts. This is why I was really excited about the Engineering strong resin.
It is a gray, again, quite thin liquid. Like the previous resin, it doesn’t feature any smell. Since it has low viscosity, it doesn’t suffer from blooming. It also holds details nicely and forms nice overhangs in the form of bridges. However, it suffers from a layer delatimation on overhangs supported only on one side:
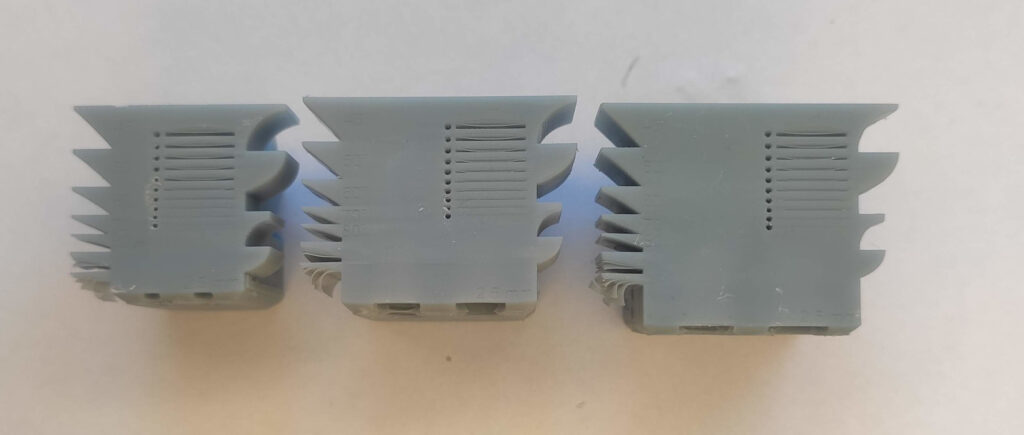
The resin has low linear shrinkage of 0.28 %. So there shouldn’t be much residual stress after printing.
From my experience, the resin is indeed strong, but it is not particularly ductile. It can withstand a lot of stress, but it doesn’t yield before failing. Also, as it claims to be a strong resin, I run my gearbox benchmark on it. You can see that all the components came out nicely. It is also very easy to tap threads in the resin – it doesn’t form dust that blocks the hole when cutting like most resins, instead, it yields nice splinters that can easily get out of the hole during tapping.
I assembled two gearboxes and I let each of them run for 20 minutes: one with and one without lubrication. The gearbox without lubrication formed a light coating of white powder. This means that the resin grinds itself like most resins. However, I have to say the effect is much less severe than on the other resins. With lubrication, I didn’t perceive a problem which is excellent. When I tried the maximum torque it can transmit, I got to 3.7 Nm. This is actually quite high for a resin! Only a few and pretty non-standard resins can beat that. See the comparison in the table below:
3D-printed Compound Planetary Gearbox
The gearbox failed on broken teeth. It could also be grinded-off tips of teeth – I cannot tell for sure. See the photos:
Overall, I am pleased with resin. It is quite strong while being easy to work with. Compared to other resins that claim to be strong (e.g., Resione M58) it is actually stronger and has a harder surface. Also, compared to them it is really thin and it doesn’t need printing at elevated temperatures. The only downside for some application might be that it doesn’t yield before failing and it fails suddenly.
The model resin
The last resin is the model resin. This resin comes in bright blue color. It has no particular smell and to my surprise, it is also very thin (even thinner than the previous resins). From the resins I use, I would compare it to Siraya Tech Simple in this regard. But this is where all the similarity ends. Due to the low viscosity, the resin is very easy to print and clean. It doesn’t suffer from blooming, and it moderately blocks UV light so it can print overhangs OKish. It cannot compare to the overhang quality of resins like Siraya Tech Fast Navy, but it performs better than most resins in this regard. The only downside of the bright blue color is that gets your cleaning bath dirty quickly. But that is only the defect of the color I had. The resin is available in many other colors.
A test piece showing how the resin can handle overhangs.
A test piece showing how the resin can handle overhangs.
The printed models are hard on the surface. When you hold it in hand, it feels like a standard resin. But when you start playing with it you will find out that it is surprisingly tough. When you apply enough force, it bends, but it doesn’t break. When you release the force, it slowly gets back in the shape. Don’t get me wrong – this isn’t a flexible resin. Just especially tough. It takes a lot of force to deform. See the videos below. For comparison, I also printed the same tire model as I printed with the flex resin. The tire printed in the model resin cannot be deformed by your hands:
When you use enough force, it will deform, but it won’t break. And when you release the stress, it slowly returns to its original shape. In the end, it can handle less stress than the Engineering strong resin, but unlike it, it doesn’t break under load. See below what happens after the same torture:
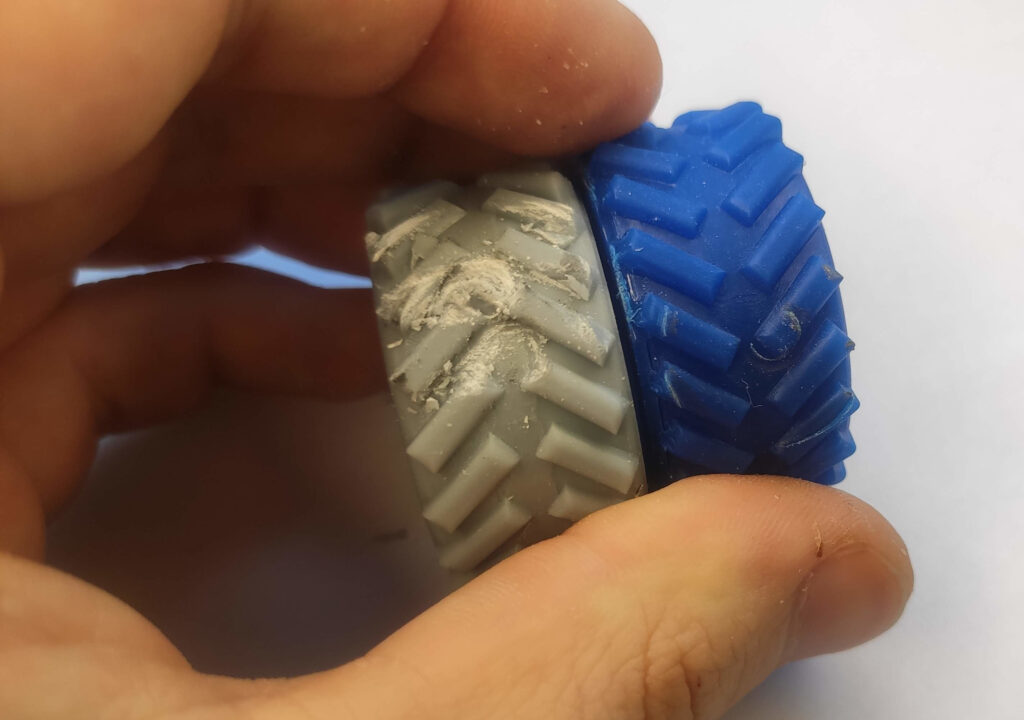
This resin has, however, quite a high shrinkage. I measured about 0.9% linear shrinkage. So if you aim at precise components, it is necessary to compensate for it.
Overall, I am really impressed with this resin. It offers an interesting mix of strongness and toughness (similarly to Siraya Tech Tenacious), but on the other hand, it is much less viscous so it is so much easier to print with! Also, compared to Tenacious, it suffers less from cross-layer curing. This resin will have a lot of interesting applications – and if someone asks what resin should they use for printing figures that survive the drop test, this is the answer. A miniature printed from this resin survives a drop test even from the 8th floor.
The resin also seems to be a suitable additive to standard resins (as a replacement for Tenacious) to reduce brittleness. And unlike Tenacious, it actually makes your resins less viscous and thus easier to print with.
Conclusion
Am I satisfied with the resins? Yeah, QTS’s claims aren’t a plain marketing talk. The resins by QTS truly have some unique properties they can offer. Also, their formula yields low-viscosity resins that are a pleasure to print with. I was amazed by the model resin’s toughness and the nice compromise between viscosity and strength of the tough resin. I think that it beats performance-wise the resin I currently considered as really good – Siraya Tech Blu (not only in strength but also in the quality of overhangs and cross-layer curing).
I only see one downside of the resins by QTS – their price. They are nearly double the price of resins that I commonly use (and, e.g., Blu). Still, they offer quite unique and nice properties and if you have a special need, they are definitely worth the money. If your goal is to print indestructible minis or you need to quickly prototype a piece from tough material I am not aware of a more suitable material than the Model resin. I guess this is also given by the fact, that QTS targets mainly professional customers at the moment. Overall, I think you get real value for the money – they offer high-performance resins, but you have to be willing to pay for that.
Recent news: My open letter to the 3D-printing community
I love the 3D-printing community, but I think there is room for improvement. Let's get better in 2023! Read the full letter.
Support my work!
If you like my work (these blog posts, my software and CAD models) and you would like to see more posts on various topics coming, consider supporting me in various ways:
- You can become my sponsor on Github.
- If you prefer, you can also become my Patreon.
- You can buy me a coffee on Ko-fi,
- or you can buy something from my Tindie store (also see below),
- Or you can just share my work!
If you are interested in knowing what I am up to and recent sneak-peaks, consider following me on social media (Twitter, Instagram, Facebook).
My store offers
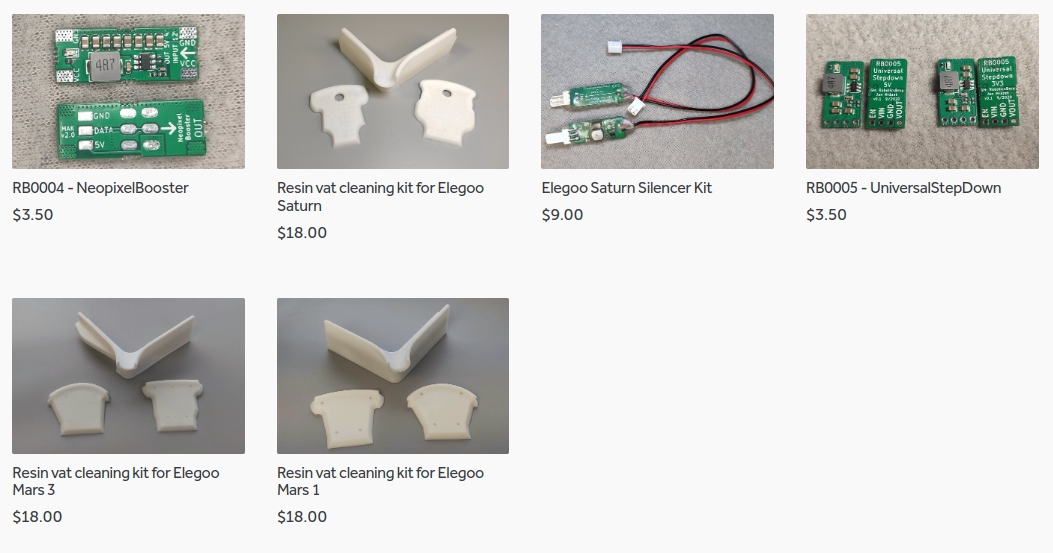
I launched new tank cleaning kits for Elegoo Saturn, Saturn S, Mars 1, and Mars 3. You can find them in my store.>
Related Posts
- Multi-planar Slicing for 3D Printers – For Both FDM and Resin
- Open letter to the 3D printing community: Let’s be better in 2023! What should we do?
- Continuous Printing On LCD Resin Printer: No More Wasted Time On Peeling? Is it possible?
- About the Successful Quest For Perfect MSLA Printer UV Backlight
>”most of the smaller companies just blindly copy the original resin formula by Autodesk ”
Wow, I didn’t know/remember that was a thing, thanks for sharing.
I know the Creative Commons license is terrible for physical objects and stuff, but, since that was under the “share alike” license, shouldn’t the other companies have to give away any derivative recipes as well?
If you’re looking for resins that actually do have some amazing properties, take a look at the BASF stuff. ST45B, for example. They also have excellent flexible resins – springy and gooy.